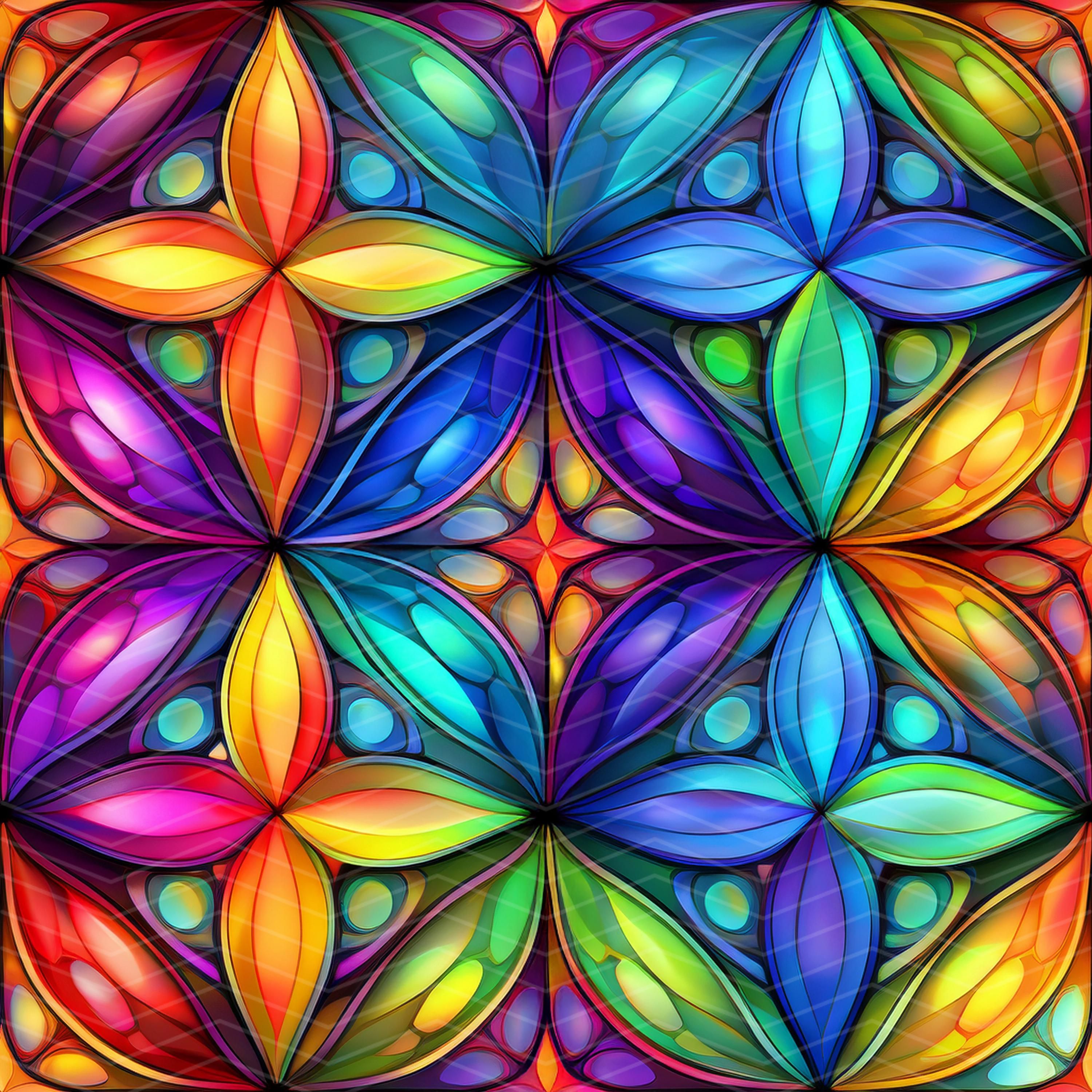
IGPS Logistics LLC Revolutionizes Auto Parts Delivery with Specialized Cowl, Grille, and Hood Protection
Orlando, FL – October 26, 2023 – IGPS Logistics LLC, a leading provider of comprehensive logistics solutions, today announced a significant upgrade to its auto parts delivery service, specifically geared towards the safe and efficient transportation of vulnerable components like cowls, grilles, and hoods. Based in Orlando, Florida, at Landmark Center One, IGPS is tackling a persistent problem in the auto parts supply chain: damage during transit. “We noticed a real need in the market,” explains a spokesperson for IGPS Logistics. “These parts – the cowl, the grille, the hood – they look tough, but they’re surprisingly susceptible to dents, scratches, and even breakage if not handled properly. And that costs everyone money – the supplier, the distributor, the repair shop, and ultimately, the customer.” IGPS Logistics, established with a vision to redefine logistics through innovation and customer-centricity, has spent the past several months developing and implementing a specialized protection and handling protocol focused on these frequently shipped, easily damaged parts. The company serves a wide range of clients across the automotive aftermarket, including parts manufacturers, distributors, and collision repair centers. They handle everything from single-piece shipments to full truckloads, offering solutions tailored to each client's needs. The Problem with Cowls, Grilles, and Hoods Let’s face it: cowls, grilles, and hoods aren’t built for a rough ride. While designed to protect the vehicle, they need protection themselves during shipping. Traditional packaging often falls short, leading to claims, returns, and delays. Cowls: These are often made of plastic or lightweight materials and can easily crack or break under pressure. Their complex shape makes stacking difficult without proper support. Grilles: Whether chrome, plastic, or metal, grilles are prone to scratches and dents. Chrome is particularly vulnerable to damage during handling. Hoods: Large and often made of aluminum or steel, hoods are susceptible to dents and bending, even with seemingly minor impacts. Their size also makes them challenging to handle and secure during transport. “We were getting feedback from our clients,” says the spokesperson. “They were saying, ‘We’re spending too much time dealing with damaged parts. It's slowing down repairs, frustrating customers, and cutting into our profits.’ We knew we had to do something different.” IGPS's Innovative Solution: A Multi-Layered Approach IGPS Logistics isn’t just slapping on some extra cardboard. They've developed a holistic solution addressing every stage of the shipping process. “It’s not just about the packaging,” explains the spokesperson. “It’s about the entire process – from how we load the parts onto the truck to how we secure them and how carefully our drivers handle them.” Here’s a breakdown of IGPS’s approach: Customized Packaging: IGPS uses a multi-layered packaging system specifically designed for cowls, grilles, and hoods. This includes: Corner Protectors: Heavy-duty corner protectors shield vulnerable edges from impact. Protective Wrapping: Parts are individually wrapped in a durable, scratch-resistant material. Custom-Fit Boxes: IGPS utilizes boxes tailored to the specific dimensions of each part, minimizing movement during transit. Padding & Dunnage: Additional padding and dunnage fill any remaining space within the box, providing maximum protection. Specialized Handling Procedures: IGPS has implemented strict handling procedures for these vulnerable parts: Dedicated Loading Zones: Parts are loaded and unloaded in dedicated zones, minimizing the risk of damage from other cargo. Trained Personnel: IGPS employees are trained in the proper handling techniques for cowls, grilles, and hoods. Securement Protocols: Parts are securely strapped and braced within the truck to prevent shifting during transit. Real-Time Tracking & Monitoring: IGPS utilizes advanced GPS tracking and monitoring technology, providing clients with real-time visibility into the location and condition of their shipments. This allows for proactive intervention in case of any potential issues. Damage Reduction Guarantee: IGPS is so confident in its new system that it’s offering a damage reduction guarantee. “We’re committed to reducing damage claims significantly,” says the spokesperson. “We want our clients to have peace of mind knowing that their parts are in safe hands.” Beyond Protection: Streamlining the Supply Chain IGPS Logistics isn’t just focused on preventing damage. They’re also working to streamline the entire supply chain. “We understand that speed and efficiency are critical in the automotive aftermarket,” says the spokesperson. “That’s why we’ve invested in technology and infrastructure to optimize our logistics processes.” IGPS offers: Just-in-Time Delivery: IGPS can deliver parts directly to repair shops or distribution centers on a just-in-time basis, minimizing inventory costs and maximizing efficiency. Cross-Docking Services: IGPS offers cross-docking services, allowing clients to consolidate shipments from multiple suppliers into a single delivery. Inventory Management: IGPS can manage clients’ inventory levels, ensuring that parts are available when and where they’re needed. Looking Ahead IGPS Logistics is committed to continuous improvement and innovation. The company is already exploring new packaging materials and handling techniques to further enhance its protection capabilities. They’re also planning to expand their specialized service to other vulnerable auto parts. “We see a real opportunity to revolutionize the auto parts logistics industry,” says the spokesperson. “We’re not just moving parts; we’re providing peace of mind and helping our clients succeed.” Contact: IGPS Logistics LLC LANDMARK CENTER ONE, 315 E. ROBINSON STREET, SUITE 520, ORLANDO, FL, 32801, UNITED STATES 210-249-8415 [Website/Contact Information - to be added]